Reflow
You can reflow a PDF to temporarily present it as a single column that is the width of the document pane. This reflow view can make the document easier to read on a mobile device or magnified on a standard monitor, without scrolling horizontally to read the text. You cannot save, edit, or print a document while it is in Reflow view. Reflow Tanklines provides hazmat and non-hazmat liquid bulk transportation solutions for customers throughout the US. We specialize in a wide range of liquid chemicals, industrial pressurized gases, fuels & gasoline, performance grade asphalts, as well as kosher food grade products. Reflow soldering is the most widely used form of soldering for PCB assembly both in mass production and for prototype PCB assembly. Reflow soldering enables is reliable and effective for all pitches of leads and pads, enabling very high quality circuit boards to be manufactured.
- Highest Yield Reflow Oven!
- Lowest Delta T on the board
- Lowest Nitrogen & Electrical Usage!
- Maintenance Free!
- At ReFlow we offer mutual funds innovative approaches to handling shareholder flow—the affordable liquidity that you need—when you need it. Our solutions, Redemption Service and NAVswap, are designed to reduce friction and performance issues due to disruptive shareholder flow.
- A reflow oven can be a small batch (box) style oven for very small lab scale operations. For larger manufacturers, an inline or conveyor belt reflow oven is the best choice. In the early days of electronics manufacturing, infrared (IR) heating technology was employed.
- VOID Free Reflow Oven – with Vacuum option
- Industry 4.0 Compatibility
Reflow Oven w/New Low Height Top Shell
The new low height top shell provides much easier access for reflow oven operators. All skins have double insulation to save up to 10-15% in reflow soldering energy loss. Internet of Manufacturing (IoM) —Smart factories, intelligent machines and networked processes through the use of cyber-physical systems. Enhanced low height heater module provides the lowest Delta Ts on the reflow oven with better air flow and uniformity! The Uniform Gas Management system eliminates “net flow” which results in nitrogen consumption reductions of up to 40%! New semi-circular heater is more robust and efficient with much longer life time.MK7 Reflow Oven | Overall Length | # of Heating Zones | # of Cooling Zones | Max PCB Width | |
---|---|---|---|---|---|
1826** | 465 cm (183″) | 8 | 2 Top (std) Bottom Cool / External Cool optional | 22″ | |
1809* | 465 cm (183″) | 9 | 2 Top (std) Bottom Cool / External Cool optional | 22″ | |
1936** | 590 cm (232″) | 10 | 3 Top (std) Bottom Cool / External Cool optional | 22″ | |
1913* | 590 cm (232″) | 13 | 3 Top (std) Bottom Cool / External Cool optional | 22″ | |
2043** | 678 cm (267″) | 13 | 3 Top (std) Bottom Cool / External Cool optional | 22″ | |
2049 | 744 cm (292″) | 15 | 4 Top (std) Bottom Cool / External Cool optional | 22″ | |
2156 | 869 cm (342″) | 17 | 5 Top (std) Bottom Cool / External Cool optional | 22″ | |
*The 1913, 1809 & 1707 Reflow Oven series have 10 inch wide heater modules for reduced liquidus time. **2043, 1936 & 1826 Reflow Oven models have 12 inch modules for profile compatibility with competitor systems. |
Selecting a Reflow Oven

There are many factors to consider when choosing a reflow oven. The type of production environment is an important factor, meaning the product mix and volume. Is it a very high volume production environment with very little change in board type or size? Or is it a very low volume production environment, with periods of low or no production, and products that vary greatly in size and weight. Are the boards particularly difficult thermally? Do they have very big components and smaller ones? How tight is the thermal process window (the difference between the minimum process temperature and the maximum allowed process temperature)? What is the required throughput of the line?
Reflow Oven Sizing
Reflow ovens are sized primarily based on the required throughput. The number of boards produced per minute in a conveyor based reflow oven is based on the belt speed, and then length of the board plus the between board spacing. The boards per minute can be doubled, tripled or even quadrupled for multi-lane systems (boards processed side by side). The reflow oven belt speed is limited by the process specification which dictates ramp rates, and time above liquidus values.
Typical solder reflow Profile Targets:
- Peak temperature = 240+/-5°C
- TAL/Time above liquidus (221) = 30 to 60 seconds
- Soak (activation) = 150 to 200°C for 0-60 seconds
- Ramps = 2.5°C/second max for heating, -1.5°C/second for cooling
Given the specification above the reflow process would require 104 seconds for ramp, 60 seconds to soak, 16 seconds to ramp to peak, and 60 seconds time above liquidus – this results in 240 seconds in the heated section of the reflow oven (4 minutes).
If the board size is 10 inches long, single lane, with 3 inch spacing and the factory requires 120 per hour (or 2 per minute) the required belt speed would be 26 inches per minute (IPM).
Flow Soldering
So with the required belt speed of 26 IPM and the process time of 4 minutes the required inches of heat would be 104”. With Reflow oven sizes of 75”, 100”, 125” or 150” heated length the best choice would be at 125” inch reflow oven. If a factory is tight on space you could consider a shorter reflow oven by processing your boards multiple lanes (dual lane or more) and slowing your belt speed, this would allow a shorter reflow oven to produce more boards.
Reflowing
How Many Zones are Needed?
The number of zones required is considerably less important than the overall oven heated length and the thermal control performance of the reflow oven. There is a balance that must be struck between complexity of operation of the oven and ability to fine tune. Reflow oven zone widths of 10 to 14 inches are standard in the industry, and are adequate for the vast majority of reflow process requirements. For lab or pilot production 6 zones are often enough. For production environments 8 zones or more should be considered.
Want to learn more? Contact BTU with any questions or to hear about the latest advancements in reflow ovens, furnaces or SMT technology.
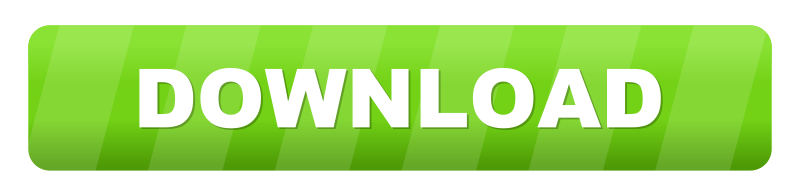